As Greta Thunberg puts it, climate change is a fact. We are dealing with science here
Those working with Arvind Kejriwal have confirmed his upcoming trip to Copenhagen for the C40 Mayors Summit to discuss ways for the capital city to reach the goals of the Paris Agreement and limit carbon emissions through green transition and climate adaptation. The environment is indeed on the agenda of industry leaders and policymakers. For whatever reasons.
Fashion, being the most polluting industry after oil, has its own share of carbon emission. The production methods to develop industrially woven fabrics adversely affect the environment so much so that almost 67% of emission from the entire supply chain happens during raw material production and initial stages of processing.
There remains a club of textile designers that stand responsible and are pushing the boundaries of what the future of textiles could be. Craftsmanship and technology have enabled designers in the recent past to develop fabrics out of anything biodegradable and sometimes things as good as soy milk!
Yes, the surprise is natural for when you are told the textile of the shirt you are wearing is made out of the orange peel. Not just that, material designers have explored a plethora of organic excess to make fabrics that are a breather for the environment and shall go back into the earth just how they were grown in the first place, i.e. naturally.
Adriana Santanocito and Enrica Arenaby have re-imagined Italy’s yearly waste of one million tonne citrus fruit peel waste that earlier required expensive waste management. Converting this resource into a textile using technology that helps extract cellulose from the peel, they were able to spin an organic yarn out of it. The textile is full of Vitamin C and essential oils, a treat for the skin.
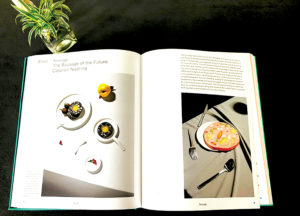
Whereas Anke Domaske, a German designer wanted to dress her father — who was suffering from cancer — with healthy fibres. While Milk protein was already transformed into fabric back in the 1930s, she devised a rather chemical-free way to do the same. Her biopolymer-based textile company, Qmilk founded in 2011 is the first man-made fibre produced without chemicals. The textile is known to be antibacterial, anti-ageing and can even help regulate blood circulation and body temperature.
Life without textiles is hard to imagine, this is why innovation in bio-based materials is more than relevant considering the position textile industry takes when it comes to environmental harm. Being a significant sector, the greenhouse gas emissions from textiles production, at 1.2 billion tonnes annually, is more than those of all international flights and maritime shipping combined. When fast fashion, that utilises a huge chunk of this textile is designed to last for not more than 10 years, we must absolutely look ahead and opt for eco-friendly materials and products.
While internationally designers have explored all kinds of bio-based materials to create materials for various purposes including fashion, the Indian design community is catching up too with respect to the local need and availability. Malai is a Kerala based studio that develops vegan leather made out of organic bacterial cellulose, grown on agricultural waste sourced from the coconut industry. Boheco and Anandi from south India have fibre variants in Hemp, Banana, Aloe Vera and Areca.
Working on fibre level is an ambitious affair and designers increasingly choose to source ready-made fabrics available in the market. A few retail shops in Delhi have followed suit the international fad for sustainable fabrics made out of soy milk, corn, lotus, banana, bamboo but their authenticity is still a question for the price they are being sold at.
While thoroughly developed textiles are a rarity, Shradha Kochhar is one of the few creatives whose learning curve has led her to explore alternative materials in fashion. A knitwear designer from Delhi, she has utilised textile made out of hemp and also developed a khadi knit for label 11.11 as part of her final year collection at NIFT. Currently based out of New York, enrolled at Parson’s Hybrid textile course, she is working on a fusion of Indian organic cotton and orange strands, exploring its restorative properties.
The fact that her grandparents had to migrate from Rawalpindi that is present-day Pakistan to now India has had a long-lasting effect on her. The textile shall utilize the narrative in its make. The variety of cotton that got left behind in the entire act of population movement shall be documented in her work.
“The idea to take up this course here in New York is to further my skill and understanding of textiles”, tells Kochhar who also developed furry knits for London based designer label Ashish’s autumn-winter 2019 collection. Back home in Delhi, she is also one half of Lota, a label she runs with her partner that repurposes textile waste from export industries into youthful separates.
As more and more people are becoming eco-conscious, it is important to maintain that we know the facts and figures clearly before acting on anything. Industrially made textiles affect the health of the textile workers, the ones who wear it and eventually the environment. Some garments, when washed, release plastic micro-constituents, of which around half a million tonnes every year contribute to ocean pollution – 16 times more than how the cosmetic industry does.
Smriti Arora (name changed), a Delhi based fashion designer who develops her own handspun and handmade textile in Chanderi, is of the view that the power lies with a buyer. “I get requests from buyers to make the same outfit in cheaper fabric to cut costs. We do not understand the harm we do to the environment to save on money”, affirms the designer.
The potential to drive change is true with the shoppers who can give their vote of confidence to sustainable products. Considering the environmental state of our planet, it is the call of the hour to consciously indulge in fashion.