At the break of dawn, Ranju wakes up to do the first round of her job – to collect cartons lying around in the streets. When the market opens around 9 am, she negotiates with shopkeepers for buying their empty cardboard boxes in bulk and consolidates her collection to take it to the dumpyard. There, several workers like her stack the cartons to be sent to Muzaffarnagar, Uttar Pradesh, for recycling.
The 34-year-old lives in the village right behind the majestic Tughlaqabad Fort in Delhi, amid heaps of garbage and in abject poverty.
Also read: At the heart of Delhi, a ‘mini Cooch Behar’ in a state of despair
For most of these villagers, scrap is the primary source of livelihood – whether it is waste paper, small cardboard boxes or bigger cartons. The majority of slum dwellers hail from Bihar.
Life amidst litter
The gigantic Tughlaqabad Fort, which once served as the symbol of power and might of the Tughlaq dynasty, draws hundreds of visitors who admire its grandeur and greatness. Little do they know that behind the historical monument live migrants from Bihar, who moved to the national capital for a “better life.”
“We moved to Delhi 12 years ago in search of better income, but now we plan to return to our village in Supaul because living here is too expensive. We used to earn around Rs 8,000 a month but now we get even less. There is hardly any work,” Ranju says.
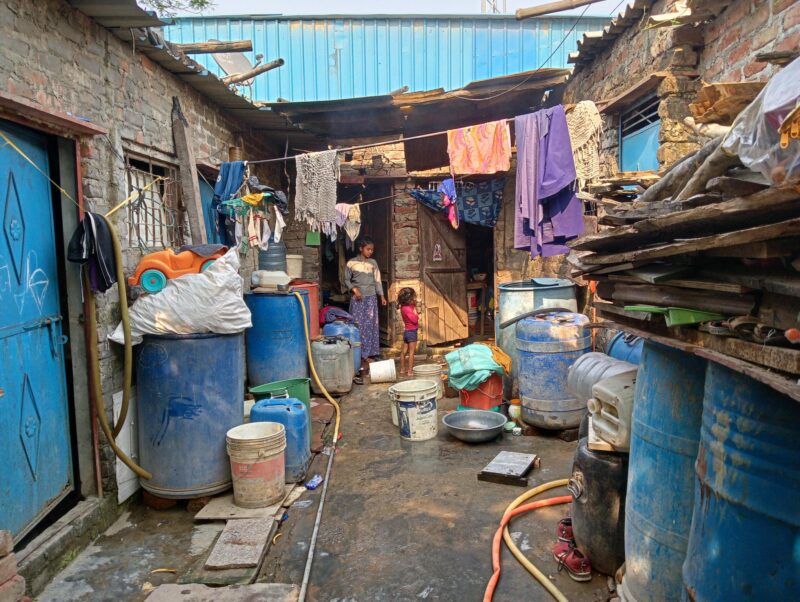
family collects
“We buy these boxes at Rs 12 per kg. The consignment goes to Muzaffarnagar only when the collection reaches 5 tonnes, otherwise we sell to the local printing press,” she adds.
Ranju lives with a family of five people. “My husband and brother-in-law do the same work. We begin early, around 5 am, so that we can wrap up by sunset because it gets pitch dark after that – there are no street lights. The poles end at the entrance of the village,” she says.
Her hutment is surrounded by garbage, which she says is “a result of visitors throwing plastic bottles, food packs from atop the fort.”
Health hazard
Manoj has been working in a box-making factory in the village for the past eight years and suffered injuries thrice. Despite his “good pay”, he has never received compensation for any of the injuries. “Thin paper often causes lacerations or cuts on your skin. Two of the three injuries were deep enough for me to take leave from work for a week. These injuries come at a cost because our leave is without pay. From the creation of pulp, to the formation and solidification of the cardboard containers, any number of safety issues can be experienced. There could also be injuries during the heating process,” he says.
Paper mills generate large volumes of dust particles, but the labourers continue working without any safety gear, not even masks.
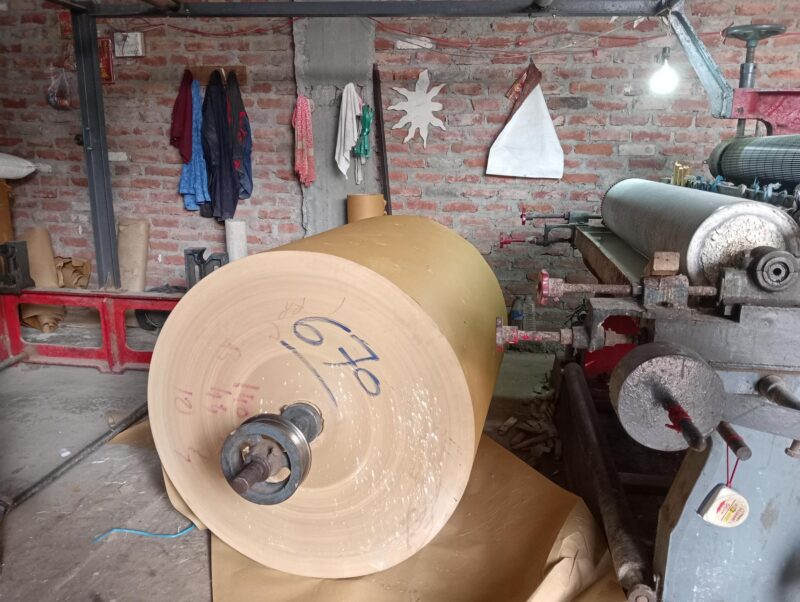
“Exposure to toluene causes eye and nose irritation. Sometimes it is severe and sometimes we get inflammation of the skin for days. For all this, we don’t ever get any compensation. But we don’t complain because the pay is good,” he concludes.
Box-making process
“People have very little idea about the kind of labour that goes behind making cardboard boxes that are a necessity in almost all households. It involves multiple stages like fluting, sandwiching, making and then boxing,” says Sudhir, a worker in the village workshop.
Corrugated cardboard is an ‘extremely versatile material’ that is used to protect, display and ship virtually all types of products. It is made using three layers of strong paper known as craft paper, which makes it strong, stiff and lightweight.
“The manufacture of corrugated packaging can be roughly classified into two processes: the containerboard combining process, which glues one or more sheets of fluted corrugating medium to one or more flat facings of linerboard; and the box manufacturing process, which is used to assemble the corrugated sheets into boxes,” he says.
Fluting refers to the middle layer of corrugated cardboard that is configured in a wave-shaped pattern of arches. Corrugated cardboard is made by sandwiching fluting between two liners. “The fluting gives the boxes their strength and helps protect merchandise from damage while in transit,” he says.
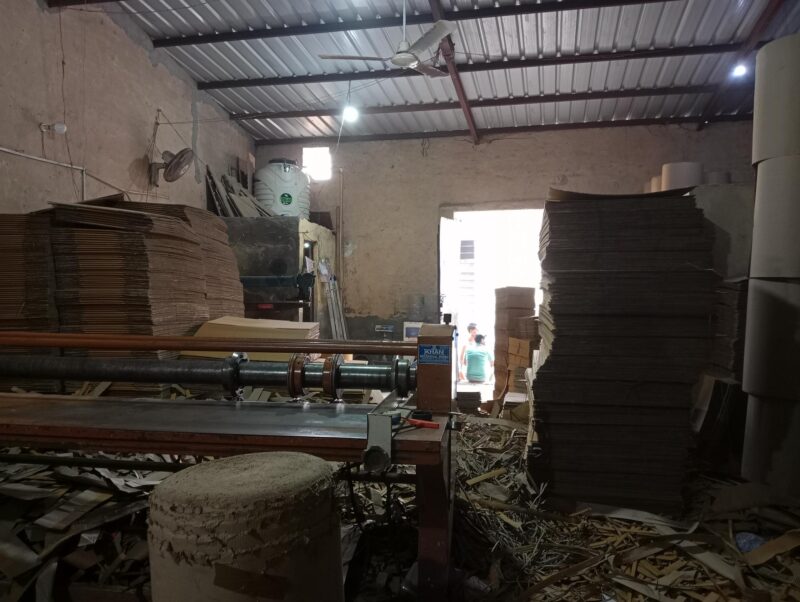
One roll is loaded into the machine to be corrugated, and a roll of liner is fed in to later be joined with the corrugated medium. A second roll of liner travels over the bridge, which is a flat structure over the corrugating rolls. The liners are adhered to the corrugated medium at a later point in the process.
A corrugating medium is pressed into a wave-like shape (flutes), then is glued to both a top sheet and a bottom sheet of linerboard. The corrugated boards are then dried, scored, cut and loaded.
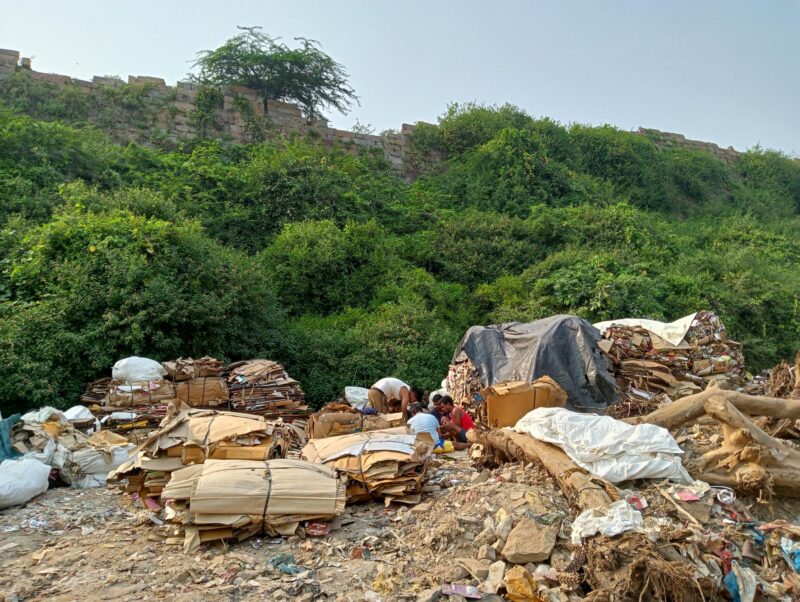
stacking cardboard into neat piles
“The machines that are used to form boxes with this glue joint method are called ‘folder gluers’. Folder gluer machines generally utilize vinyl acetate emulsion adhesives, in particular, those adhesives containing di-n-butyl-phthalate and xylene (or toluene), in order to improve heat resistance, cold resistance and drying speed,” Sudhir explains.
However, he exclaims, “But, for all this, we hardly get Rs 10,000 a month. Most of us are the only earning members of our household. We hardly survive on this.”
Follow us on:
Instagram: instagram.com/thepatriot_in/
Twitter: twitter.com/Patriot_Delhi
Facebook: facebook.com/Thepatriotnewsindia